London PAT Testing: The Importance of Portable Appliance Testing (PAT)
Portable Appliance Testing (PAT) is a crucial process that ensures the safety and compliance of electrical equipment in the workplace. It plays a vital role in maintaining health and safety standards and adhering to fire risk policies. This article will delve deeper into the significance of PAT, its legal responsibilities, and the key legislation governing it.
Table of Contents
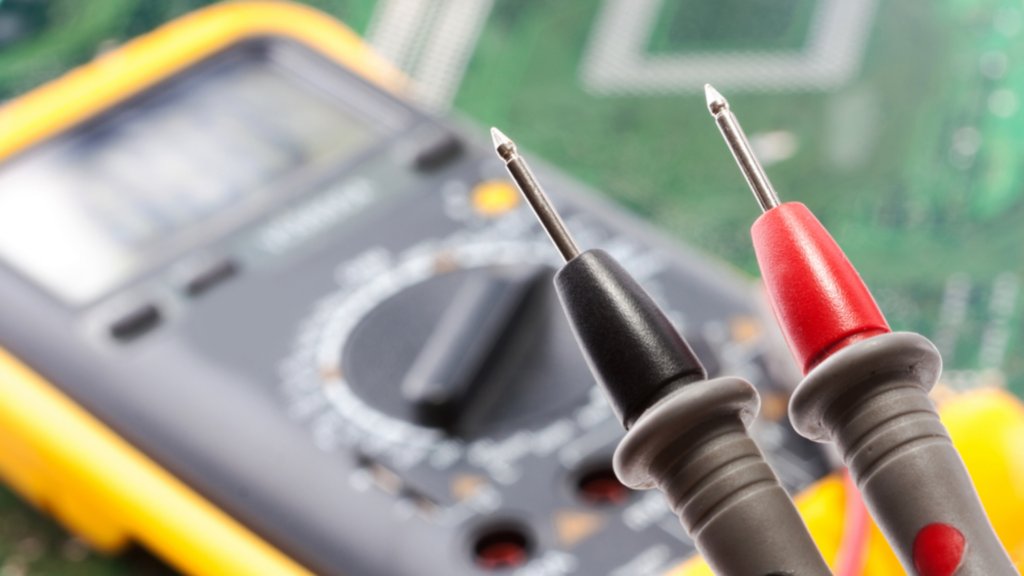
Why PAT is Essential
The Health and Safety Executive (HSE) reports that 25% of all electrical accidents involve portable appliances. This statistic highlights the potential risks associated with portable electrical devices. Annually, around 1,000 workplace accidents involving electric shocks or burns are reported to the HSE, with approximately 15 being fatal. These figures underscore the importance of regular testing and maintenance of portable appliances to prevent accidents and ensure a safe working environment.
Legal Responsibilities Under Electrical Regulations
Employers, employees, and self-employed individuals are legally required to use portable electrical equipment safely. This involves adopting a systematic maintenance, inspection, and testing approach as mandated by various regulations. The Health and Safety at Work Act (1974) emphasises the duty of workplace managers, business owners, or appointed persons to fulfil these obligations.
London PAT Testing: Key Legislation Related to Electrical Testing and Certification
Several key pieces of legislation govern the testing and certification of electrical equipment:
- Health & Safety at Work Act 1974: This act imposes a duty on employers, landlords, and users of electrical equipment to ensure its safety. It mandates the maintenance of records and certification to demonstrate compliance.
- Management of Health & Safety at Work Regulations 1999: These regulations require employers to conduct thorough risk assessments for their employees and others affected by their operations. This includes assessing the risks associated with electrical equipment.
- Provision and Use of Work Equipment Regulations 1998: These regulations mandate that work equipment be kept in good working order and condition. They cover all work equipment, including portable electrical items, which must be tested and certified. Fixed electrical installations are excluded from this regulation.
- Electricity at Work Regulations 1989: This regulation specifies that all electrical systems must be constructed and maintained to prevent danger as much as reasonably practicable. It encompasses a broad range of electrical equipment connected to a standard power source.
Scope of Legislation
These regulations collectively apply to all electrical equipment used in the workplace, from power distribution systems to the smallest portable devices. Regular inspection and testing of all types of electrical equipment within work environments is a clear requirement. To comply with these regulations, all new appliances introduced into the workplace must undergo Portable Appliance Testing as recommended by a qualified technician.
Benefits of PAT
- Risk Mitigation: Regular London PAT Testing helps identify potential hazards before they cause harm, reducing the risk of electrical accidents.
- Legal Compliance: Complying with PAT regulations ensures that businesses meet their legal obligations, avoiding potential fines and legal issues.
- Equipment Longevity: Regular testing and maintenance can extend the lifespan of electrical equipment by identifying issues early and allowing for timely repairs.
- Peace of Mind: Knowing that all electrical equipment is regularly tested and certified provides peace of mind for employers, employees, and other stakeholders.
PAT Testing Process
The PAT testing process involves several steps:
- Visual Inspection: The technician visually inspects the appliance for any obvious signs of damage or wear.
- Electrical Testing: Various tests are conducted using specialized equipment to check for issues such as earth continuity, insulation resistance, and polarity.
- Labelling: Once an appliance passes the tests, it is labelled with a sticker indicating the test date and when the next test is due.
- Record Keeping: Detailed records are maintained for each appliance tested, including test results and any remedial actions taken.
Conclusion
Portable Appliance Testing is essential for ensuring the safety and compliance of electrical equipment in the workplace. By adhering to legal responsibilities and conducting regular testing, businesses can mitigate risks, comply with regulations, extend the lifespan of their equipment, and provide a safer working environment for everyone involved.
Remember, safety should always be a top priority in any workplace. Regular PAT testing is a proactive step towards achieving this goal.
0 Comments